Artykuł sponsorowany
Czym się kierować przy wyborze grubości blachy trapezowej?
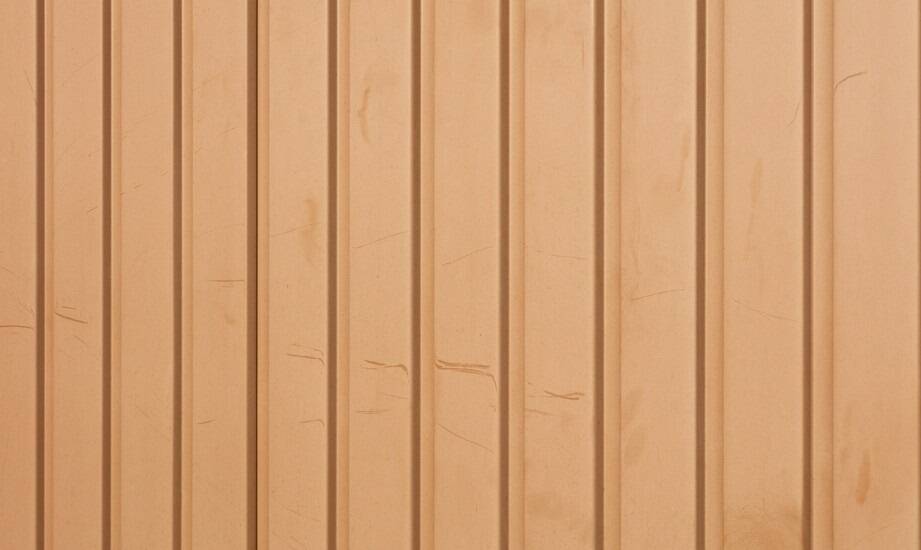
Wybór odpowiedniej grubości blachy trapezowej to kluczowy element podczas planowania budowy dachu, elewacji czy innych konstrukcji. Grubość blachy wpływa bowiem na jej wytrzymałość, trwałość oraz estetykę. W niniejszym artykule przedstawimy ogólną charakterystykę blachy trapezowej, opiszemy podział ze względu na grubość oraz podpowiemy, jak dobrać właściwą grubość w zależności od zastosowania.
Przeczytaj również: Jaki powinien być solidny producent blach trapezowych?
Ogólna charakterystyka blachy trapezowej
Blacha trapezowa to popularny materiał budowlany, który charakteryzuje się wyjątkową lekkością, wytrzymałością oraz prostotą montażu. Jej nazwa pochodzi od kształtu przekroju poprzecznego, który przypomina trapez. Blacha trapezowa wykonana jest najczęściej ze stali ocynkowanej, pokrytej powłoką ochronną z poliestru, puralu lub plastizolu. Dzięki temu jest odporna na korozję, promieniowanie UV oraz działanie czynników atmosferycznych. Wszystkie te cechy sprawiają, że od lat cieszy się zainteresowaniem jako przystępne cenowo, a przy tym jakościowe pokrycie dachowe zarówno w zastosowaniach prywatnych, jak i komercyjnych.
Przeczytaj również: Jakie cechy powinien mieć profesjonalny producent blachy trapezowej?
Klasyfikacja blachy trapezowej ze względu na grubość
Blachy trapezowe można podzielić na kilka grup ze względu na ich grubość. Jak wyjaśnia producent blachy trapezowej, grubość blachy mierzy się w milimetrach (mm) i jest jednym z głównych parametrów wpływających na jej wytrzymałość oraz zastosowanie. Wyróżniamy następujące klasy grubości blach trapezowych, które są najczęściej stosowane w budownictwie i przemyśle.
Przeczytaj również: Jak wybrać dobrego producenta blachy trapezowej t-5?
-
Blachy cienkowarstwowe - mają grubość od 0,3 do 0,5 mm. Są to lekkie blachy o niewielkiej wytrzymałości, stosowane głównie jako elementy wykończeniowe, np. do elewacji czy ścianek działowych.
-
Blachy średniowarstwowe - mają grubość od 0,5 do 0,7 mm. Są to blachy o większej wytrzymałości niż cienkowarstwowe, ale nadal nie są przeznaczone do konstrukcji nośnych. Stosuje się je np. do pokrycia dachów o niewielkim kącie nachylenia czy do budowy hal magazynowych.
-
Blachy grubowarstwowe - mają grubość powyżej 0,7 mm. Są to blachy o dużej wytrzymałości, które można stosować w konstrukcjach nośnych oraz tam, gdzie wymagana jest duża odporność na obciążenia. Przykładem zastosowania blach grubowarstwowych są dachy o dużym kącie nachylenia czy konstrukcje stalowe.
Grubość blachy trapezowej a konkretne zastosowania
Wybór odpowiedniej grubości blachy trapezowej zależy przede wszystkim od jej przeznaczenia oraz wymagań stawianych przez inwestora. W przypadku dachów o niewielkim kącie nachylenia, gdzie nie ma dużego obciążenia śniegiem czy wiatrem, można zastosować blachy średniowarstwowe. Natomiast w przypadku dachów o dużym kącie nachylenia, gdzie obciążenie jest większe, warto zainwestować w blachy grubowarstwowe.
Podobnie jest z elewacjami - jeśli mają one pełnić jedynie funkcję estetyczną i nie są narażone na duże obciążenia, można zastosować blachy cienkowarstwowe. W przypadku konstrukcji nośnych lub hal magazynowych, gdzie wymagana jest duża wytrzymałość materiału, najlepszym wyborem będą blachy grubowarstwowe.
Warto również pamiętać o innych czynnikach wpływających na wybór grubości blachy trapezowej, takich jak sam rodzaj materiału (np. stal ocynkowana czy aluminium), sposób montażu na dachu (np. na łatach drewnianych czy stalowych) czy wymagania dotyczące izolacji termicznej i akustycznej. Ostateczny wybór należy do inwestora, który powinien uwzględnić wszystkie te aspekty oraz koniecznie skonsultować się z fachowcami w celu uzyskania optymalnego rozwiązania dla swojego konkretnego zastosowania.